Choosing the right manufacturing process isn't just about rolling the dice; it's a strategic decision that can significantly impact the characteristics and performance of the final product.
First, let's break down the complexity. When it comes to manufacturing, you need three key factors: design, material, and process. Each has its own unique strengths and quirks, and they all need to work together harmoniously.
Now,
molybdenum copper alloy long tubes are no ordinary product. They're designed to withstand high temperatures and corrosive environments, making them the preferred choice for applications in aerospace, electronics, and more. But how do we ensure they meet these demanding requirements?
Enter the manufacturing process. Whether it's casting, welding, or something in between, the process we choose can determine the success or failure of the final product. Let's take a closer look at how each factor affects our molybdenum copper alloy long tubes. For example, casting involves pouring molten metal into a mold to form the desired shape. This process offers excellent design flexibility and can easily produce complex geometries. However, it may introduce porosity or other defects that could compromise the mechanical properties of the tubes. On the other hand, welding joins two or more metal pieces together using heat and pressure. While welding can create strong bonds, it may also introduce residual stress or heat-affected zones that could affect the tubes' performance, especially in high-temperature environments.
So, which process is best for our molybdenum copper alloy long tubes? It depends on various factors, including the specific requirements of the application, the desired performance of the final product, and even the expertise of the manufacturing team.
But we're not done yet. We also need to consider the material itself. Molybdenum copper alloys are renowned for their high thermal conductivity, low thermal expansion, and excellent mechanical strength. However, different manufacturing processes may alter these properties to varying degrees. For example, casting may introduce impurities or grain boundaries that reduce the tubes' thermal conductivity. On the other hand, welding may change the material's microstructure, affecting its mechanical strength or dimensional stability.
How do we navigate these complexities and make wise decisions? That's where task-based process selection comes into play. By systematically matching design requirements with the capabilities of various manufacturing processes, we can determine the best approach for our molybdenum copper alloy long tubes. But wait, there's more. We can't ignore the role of modeling in this process. Modeling allows us to predict how different manufacturing processes will affect the tubes' properties and performance, enabling us to make informed decisions without relying solely on trial and error.
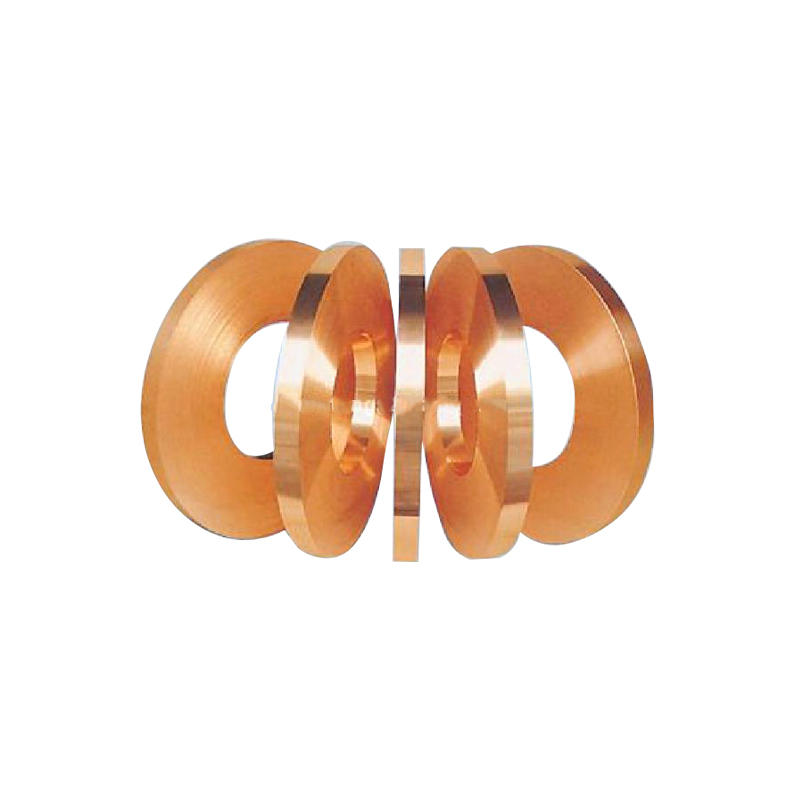