Machining: Machining tungsten alloy plates typically requires specialized equipment and cutting tools designed for hard and tough materials. Common machining techniques for tungsten alloy include turning, milling, drilling, and grinding. Carbide or diamond cutting tools with high cutting speeds and feeds are often used to achieve precise cuts and finishes. Lubrication and cooling systems may also be necessary to prevent tool wear and overheating during machining.
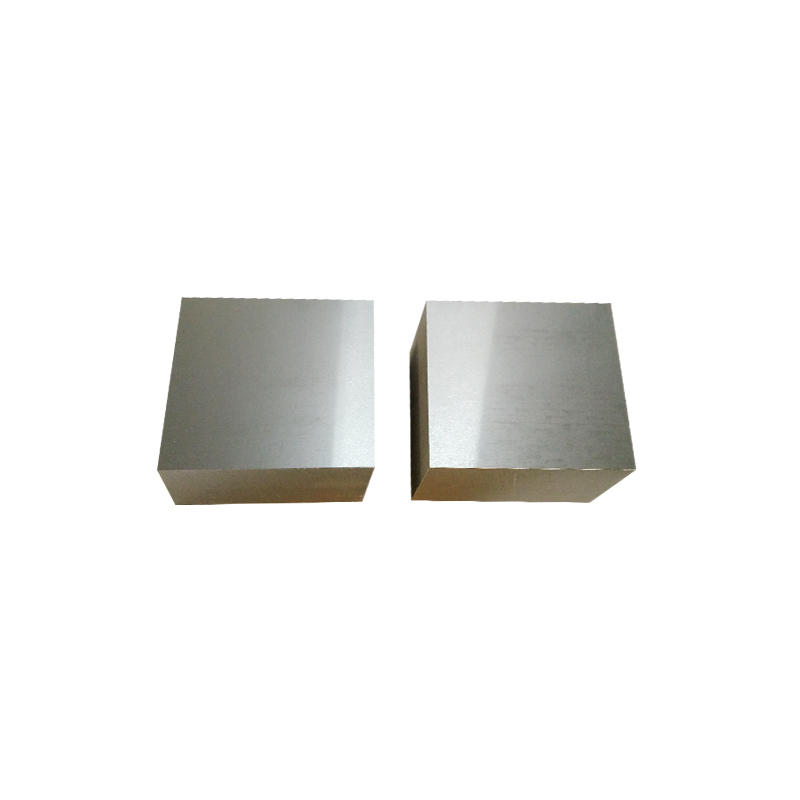
Cutting: Tungsten alloy plates can be cut using various cutting methods, including sawing, shearing, laser cutting, or waterjet cutting. Abrasive cutting techniques, such as abrasive waterjet cutting or abrasive sawing, are often preferred for tungsten alloy due to their ability to produce clean, precise cuts without generating excessive heat or causing material deformation.
Welding: Welding tungsten alloy plates can be challenging due to their high melting point and thermal conductivity. Tungsten inert gas (TIG) welding, also known as gas tungsten arc welding (GTAW), is commonly used for welding tungsten alloy plates. TIG welding provides precise control over the welding arc and allows for the use of filler materials to achieve strong, durable welds. Preheating the plates and using suitable welding parameters are essential for achieving successful welds without cracking or distortion.
Fabrication: Fabricating tungsten alloy plates into custom shapes and components may require a combination of machining, cutting, bending, forming, and welding processes. Advanced fabrication techniques, such as hot forging or powder metallurgy, may also be used to produce complex shapes or achieve specific material properties. Proper planning, tool selection, and process optimization are essential for ensuring efficient and accurate fabrication of tungsten alloy plates.
It's important to note that working with tungsten alloy plates requires careful consideration of safety precautions, such as proper ventilation, dust control, and personal protective equipment (PPE), due to the potential hazards associated with machining and handling hard and dense materials. Additionally, consulting with experienced professionals or tungsten alloy specialists can provide valuable guidance and expertise for machining, cutting, welding, and fabricating tungsten alloy plates to meet specific requirements and applications.