The application of molybdenum wire is widespread in thermal equipment. Due to its ability to maintain good physical and chemical properties in high-temperature environments,
molybdenum wire is commonly used as heating elements, electrodes, support structures, and other key components. For example, in high-temperature equipment such as smelting furnaces, heat treatment furnaces, and electron beam melting furnaces, molybdenum wire plays an important role. The ability of molybdenum wire to resist high-temperature oxidation and corrosion is mainly due to its own chemical properties and possible surface treatment measures.
Molybdenum is a metal with relatively stable chemical properties, exhibiting good corrosion resistance to most acids, alkalis, and salts at room temperature. In an oxidizing environment, the surface of molybdenum forms a dense oxide film, which can prevent further oxidation reactions, thus protecting the molybdenum wire from oxidation. The oxide molybdenum generated itself is also a high-temperature stable compound, capable of maintaining its structure and performance stability at high temperatures. This means that even under continuous high-temperature exposure, the oxide molybdenum layer is not easily cracked or peeled off, thus continuously providing protection for the molybdenum wire. The self-protective mechanism of molybdenum wire allows it to maintain its original performance even at high temperatures. Even if the oxide film is damaged or broken during high-temperature operation, molybdenum wire can quickly reform the oxide film, restoring its antioxidant performance and maintaining stable performance during operation.
To enhance the antioxidant and corrosion resistance of molybdenum wire at high temperatures, various surface treatment measures are usually adopted. For example, a layer of antioxidant coating such as aluminum oxide or silicon nitride can be coated on the surface of molybdenum wire. These coatings can form a protective barrier at high temperatures, preventing oxygen and corrosive media from directly contacting the molybdenum wire, thereby extending its service life. The antioxidant and corrosion resistance of molybdenum wire can also be optimized by controlling its purity, grain size, and adding alloying elements. High-purity molybdenum wire has better antioxidant performance, while molybdenum wire with finer grains has higher corrosion resistance. Meanwhile, during the manufacturing process of molybdenum wire, its performance can be enhanced by adding appropriate amounts of alloying elements. For example, adding small amounts of chromium (Cr) or aluminum (Al) can form more stable oxides with oxygen, further enhancing the antioxidant protection layer on the surface of molybdenum wire.
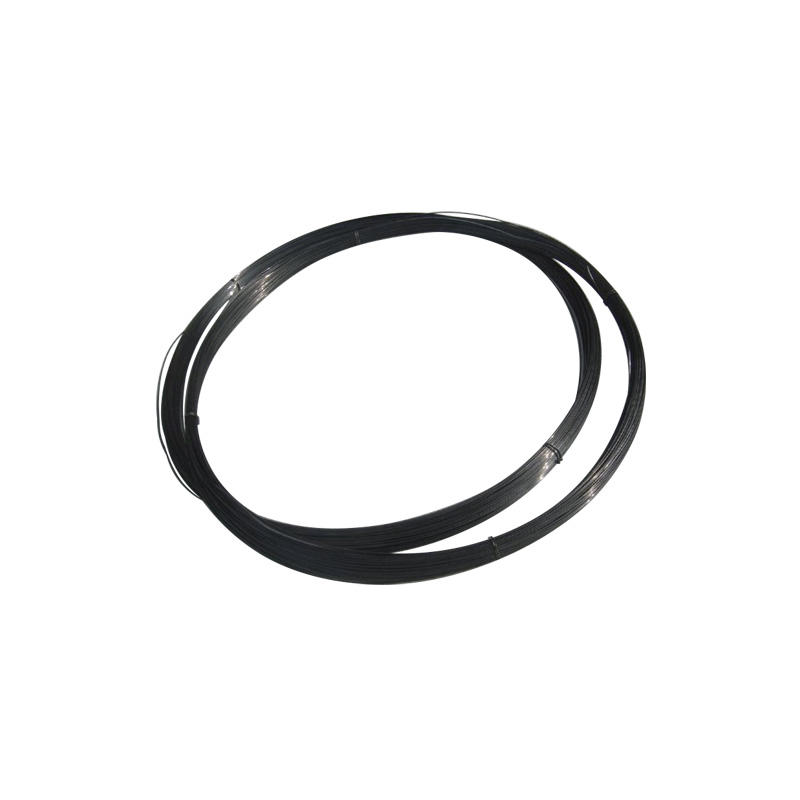